
Aruwa Medical & Dental Supplies Corniche St. Abu Dhabi Marine Sports Club, Abu Dhabi, UAE
+971561685296
Manufaturing and Design
The Made-In-Japan Products
All products in the Mytis Arrow Implant System are manufactured domestically in Japan.
Now in fields related to implantology, “the Made-In-Japan products” (including titanium, precision NC lathes, and zirconium), which are manufactured by taking advantage of the Japanese industrial and technical powers, are internationally essential and involved in various production processes. Mytis Arrow Implants have been manufactured with world-renowned, state of-the-art technology.



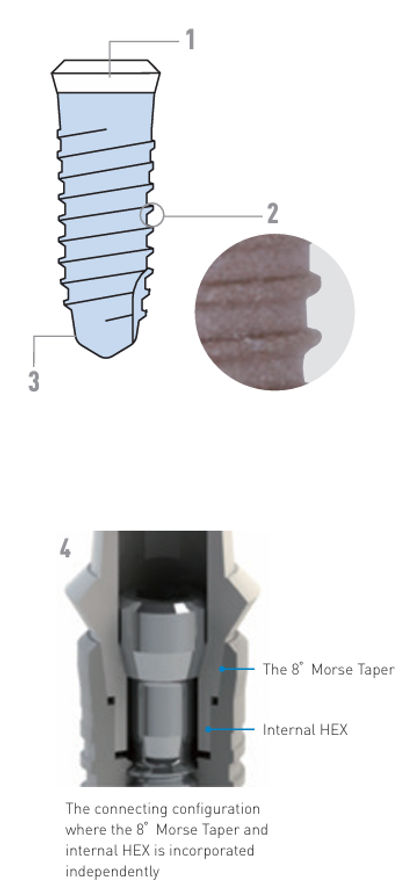
Design
1- Mirror finished part
Barrel-polishing process provides a mirror-like finish for reduced roughness to 1 μ m or less to secure the seal and tight attachment to the gingiva and to prevent postoperative infection.
2 – Dimensions of the thread
A trapezoidal thread with a 0.25mm thread depth and 0.8mm thread pitch is designed to maximize resistance during placement and to maximize retention after placement, which is the most appropriate thread shape for bone strength of Asian people.
● Thread pitch of 0.8mm An early initial fixation can be achieved.
● Thread depth of 0.25mm and R-shaped in the apical portion An early osteointegration can be achieved. As the thread is designed to give less damages to bones, an early treatment can be realized.
3 – Shape in the apical portion
The 9° tapered-shape in the apical portion is designed to reduce resistance during insertion and to help smooth and secure insertion without motion.
4 – The 8° Morse Taper / HEX Connection Design
The connection system of the 8° Morse taper and internal HEX is incorporated into the Mytis Arrow Implant and designed to secure rigid connection between implants and abutments.
The 8° Morse taper connection design has been internationally employed in many implant systems and has demonstrated excellent fatigue strength under prolonged and cyclic stress.